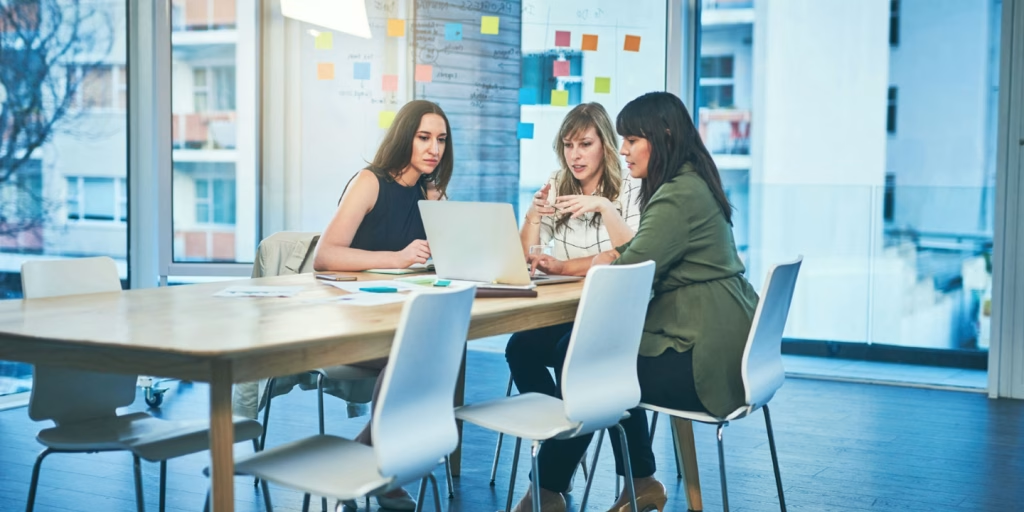
Implementing, Monitoring, and Maintaining a Quality Management System: Ensuring Long-term Success
A well-designed Quality Management System (QMS) is essential for organisations that seek to ensure consistency, meet customer expectations, and drive continuous improvement. However, designing a QMS is just the beginning; its successful implementation and maintenance are crucial for long-term success.
This guide will explore the steps necessary to effectively implement, monitor, and maintain your QMS.
Implementing Your QMS
Training and Communication
One of the most important aspects of QMS implementation is ensuring that all staff members are properly trained. Employees need to understand not only the processes outlined in the QMS but also their roles in upholding quality standards. Clear communication across all levels of the organisation is vital to ensure buy-in.
For instance, conducting training sessions or workshops tailored to different departments can make employees feel involved and knowledgeable about their specific contributions to the system.
Additionally, having accessible resources like manuals and visual guides can further reinforce learning.
Pilot Testing
Before rolling out the QMS across the entire organisation, conducting a pilot test in a smaller, controlled environment helps identify potential issues and smooth out any inefficiencies. For example, a retail company might pilot test their QMS in a single store or region to evaluate how well processes are implemented and what adjustments are needed.
The feedback gathered from this phase will allow for modifications and refinements, ensuring a more seamless implementation on a larger scale.
Rollout
Once the pilot test has been refined, it’s time for full-scale implementation. A phased rollout may be appropriate for larger organisations, starting with key departments before expanding to the entire company.
For instance, a manufacturing company could begin QMS implementation within its production department, ensuring processes are stable before moving to other departments like procurement and logistics.
Throughout the rollout, maintain open channels of communication with staff, provide ongoing support, and address any concerns promptly to ensure a smooth transition.
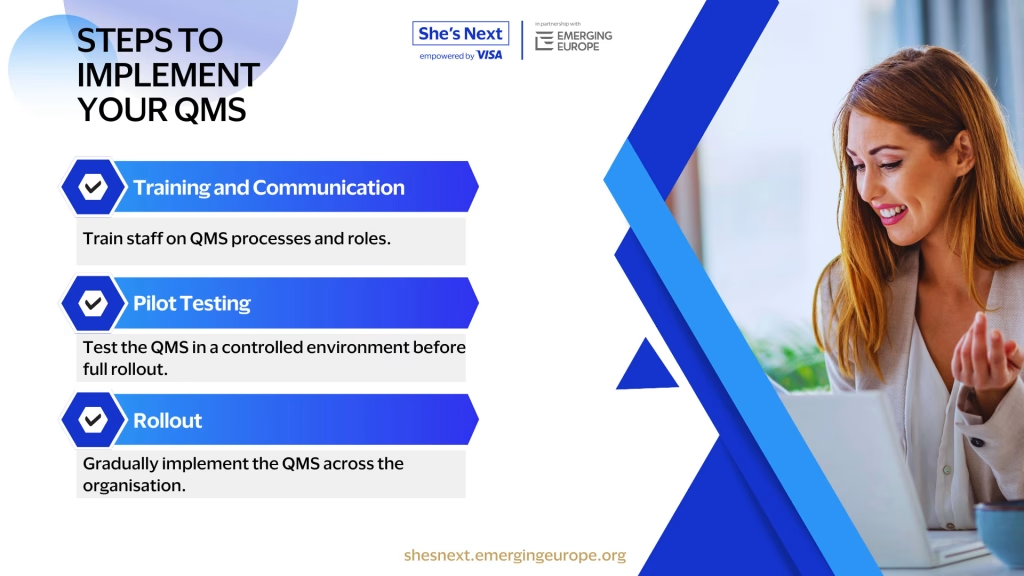
Responses