
Implementing Total Quality Management (TQM): A Step-by-Step Guide
Total Quality Management (TQM) is a comprehensive approach to improving business performance by ensuring that every aspect of the organisation is focused on quality. TQM involves all employees, from management to frontline staff, in the process of continuous improvement.
The benefits of TQM include enhanced customer satisfaction, lower operational costs, and increased efficiency.
This guide provides a six-step framework for implementing TQM in your organisation.
Understand the Fundamentals of TQM
TQM is based on several core principles that serve as the foundation for quality improvement across the organisation:
Customer Focus: The primary goal of TQM is to meet or exceed customer expectations. Everything revolves around understanding customer needs and delivering quality products or services.
Continuous Improvement: TQM requires ongoing efforts to improve processes, products, and services. It is not a one-time initiative but a long-term commitment to excellence.
Employee Involvement: For TQM to be successful, every employee must be involved in the process. From top management to entry-level staff, everyone has a role to play in maintaining and improving quality.
Management commitment is critical to the successful implementation of TQM. Leaders must set an example by promoting quality as a core value, providing resources for quality initiatives, and supporting employees in their efforts to make improvements.
Assess Your Current Practices
Before implementing TQM, it’s essential to assess your current quality practices. This helps identify areas that need improvement and where TQM can add the most value.
Start by conducting a thorough evaluation of your organisation’s current processes, procedures, and outcomes.
Tools to Consider:
SWOT Analysis: A SWOT analysis (Strengths, Weaknesses, Opportunities, Threats) can help you understand the internal and external factors affecting your organisation’s quality performance.
Quality Audits: Conducting internal or external quality audits will provide an objective assessment of how well your current processes align with quality standards and where gaps exist.
Develop a TQM Plan
Once you’ve assessed your current practices, the next step is to create a structured TQM plan. The plan should include:
Specific Goals: Define measurable goals such as improving product quality, reducing defects, or enhancing customer service.
Strategies and Actions: Detail the strategies you’ll use to achieve your quality goals. For example, you might implement new processes for better customer feedback collection or focus on improving supplier quality.
Alignment with Strategic Objectives: Ensure that the TQM plan is aligned with your company’s overall business objectives. For instance, if your goal is to improve customer retention, your TQM efforts should focus on enhancing the quality of your customer service.
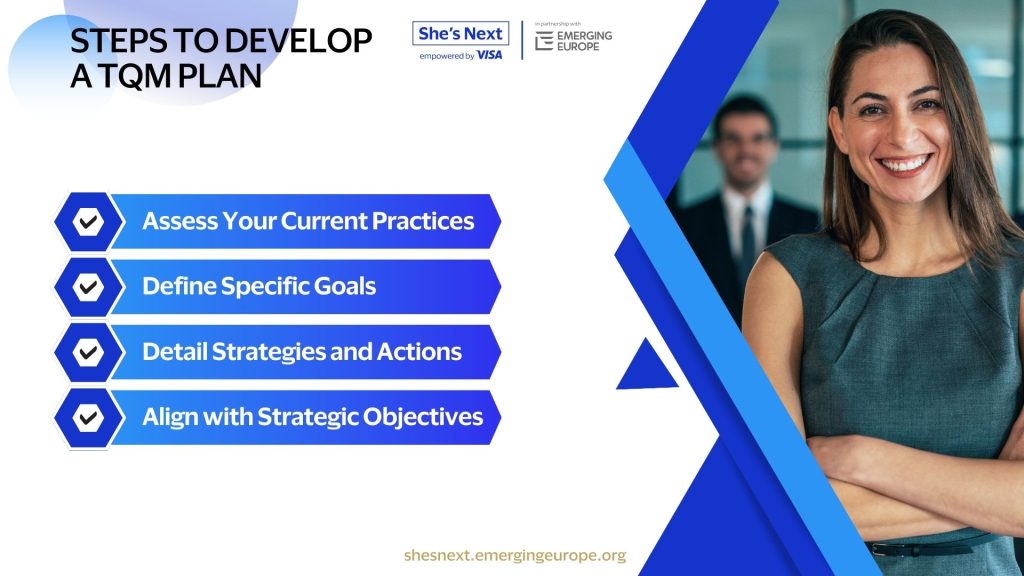