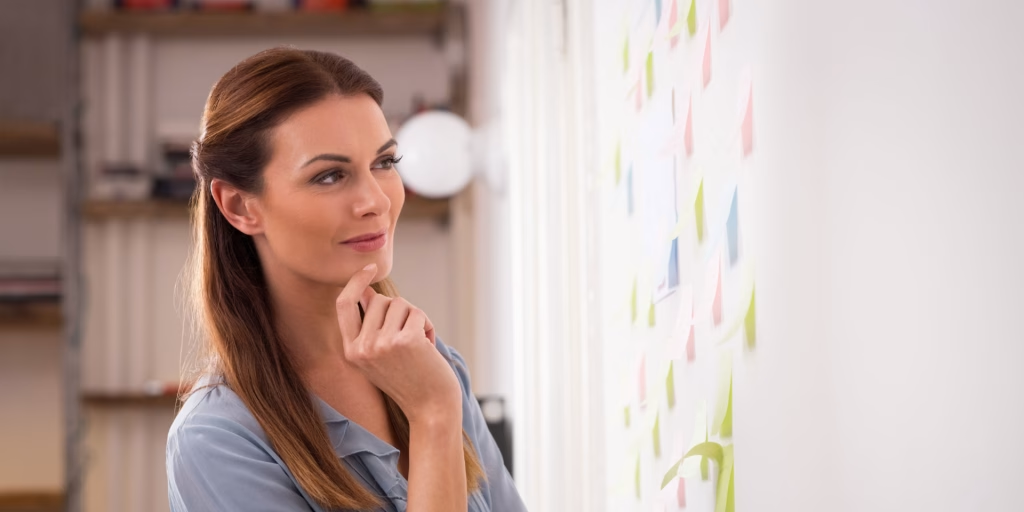
Understanding and Designing a Quality Management System: From Basics to Blueprint
A Quality Management System (QMS) is a structured framework that guides an organisation in meeting customer requirements and improving efficiency. By establishing clear processes and responsibilities, a QMS ensures that products or services consistently meet quality standards.
The benefits of a QMS are vast, ranging from improved customer satisfaction to increased operational efficiency and compliance with international standards.
Understanding the Basics of QMS
At its core, a QMS is built on several key components that support an organisation’s commitment to quality:
Document Control
Ensures that all documents related to processes, policies, and procedures are properly managed, updated, and accessible to relevant personnel.
Quality Policy
A formal statement that reflects the organisation’s commitment to quality and sets the tone for all quality-related efforts.
Quality Objectives
Measurable targets aligned with the organisation’s goals that are critical in tracking the effectiveness of the QMS. When establishing a QMS, it’s essential to follow recognised standards such as ISO 9001, a globally accepted benchmark that outlines the requirements for a QMS. Following standards such as ISO 9001 ensures that your system aligns with best practices and can enhance both internal processes and external credibility.
Planning for QMS Implementation
Needs Assessment
Before implementing a QMS, it’s important to conduct a thorough needs assessment to identify areas within the organisation that would benefit most from structured quality control.
For instance, a small manufacturer might identify issues in product consistency, while a service-based business might focus on improving client satisfaction through standardised processes.
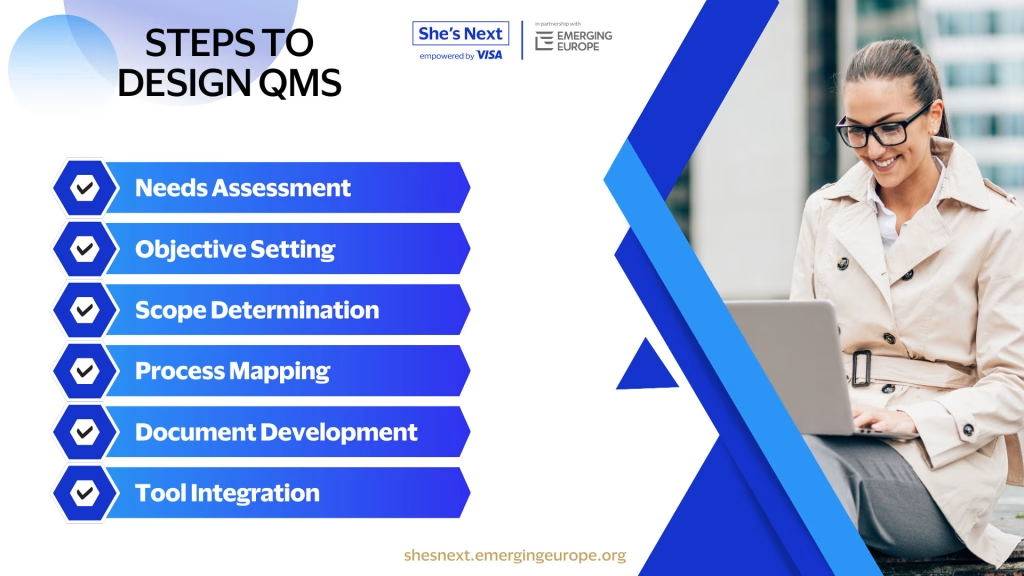
Responses